Understanding What is Porosity in Welding: Causes and Solutions
Understanding What is Porosity in Welding: Causes and Solutions
Blog Article
Porosity in Welding: Identifying Common Issues and Implementing Best Practices for Prevention
Porosity in welding is a pervasive concern that usually goes undetected until it creates substantial issues with the integrity of welds. In this conversation, we will explore the vital aspects contributing to porosity development, examine its detrimental results on weld performance, and review the finest practices that can be embraced to lessen porosity incident in welding processes.
Common Reasons of Porosity
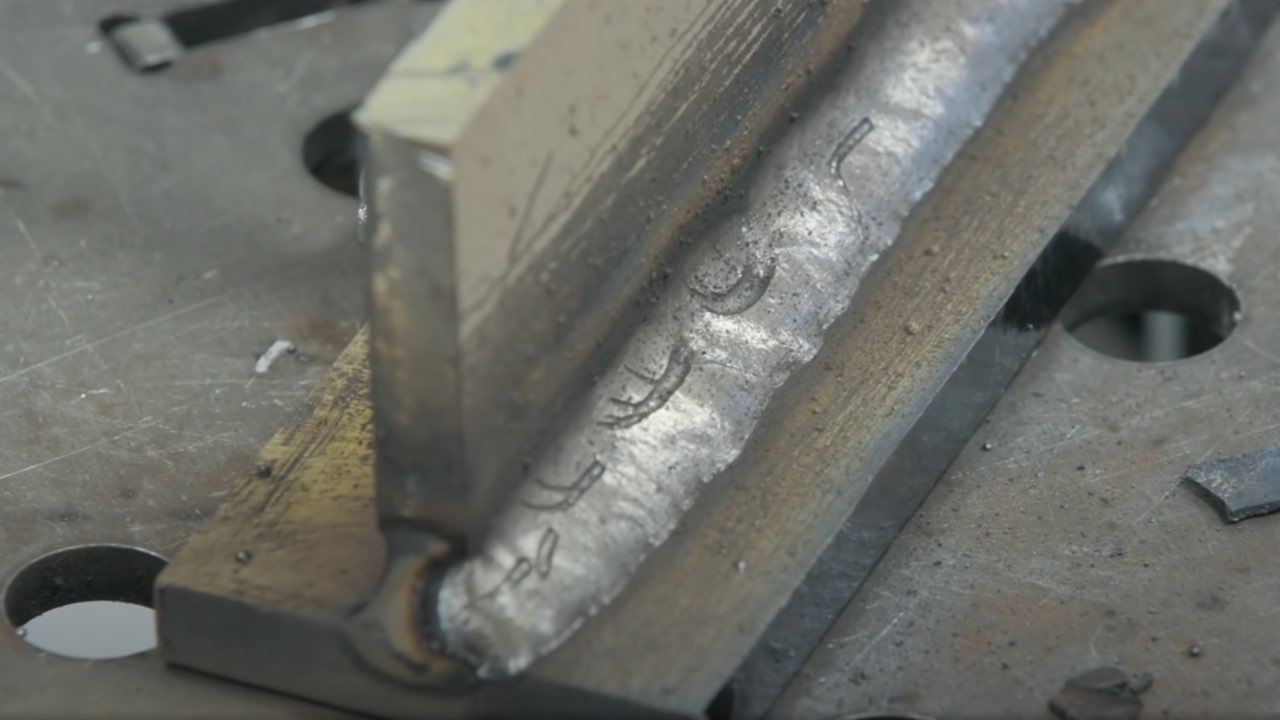
One more constant offender behind porosity is the visibility of contaminants on the surface area of the base metal, such as oil, grease, or corrosion. When these contaminants are not successfully removed before welding, they can evaporate and become caught in the weld, creating problems. Furthermore, utilizing unclean or wet filler materials can introduce contaminations into the weld, adding to porosity problems. To alleviate these usual sources of porosity, complete cleaning of base steels, correct shielding gas option, and adherence to optimum welding criteria are necessary methods in attaining top quality, porosity-free welds.
Impact of Porosity on Weld Top Quality

The visibility of porosity in welding can significantly compromise the architectural integrity and mechanical homes of welded joints. Porosity develops spaces within the weld metal, damaging its general strength and load-bearing ability.
One of the primary repercussions of porosity is a reduction in the weld's ductility and toughness. Welds with high porosity degrees tend to show lower impact stamina and reduced capability to deform plastically prior to fracturing. This can be particularly concerning in applications where the bonded components are subjected to vibrant or cyclic loading conditions. In addition, porosity can restrain the weld's ability to effectively send forces, leading to premature weld failing and potential security dangers in important structures.
Best Practices for Porosity Avoidance
To boost the architectural integrity and quality of welded joints, what certain measures can be carried out to decrease the incident of porosity during the welding process? Porosity prevention in welding is crucial to ensure the honesty and toughness of the last weld. One efficient technique appertains cleaning of the base steel, removing any kind of contaminants such as rust, oil, paint, or moisture that could lead to gas entrapment. Making certain that visit this website the welding tools remains in great problem, with clean consumables and suitable gas flow rates, can likewise significantly minimize porosity. In addition, preserving a secure arc and regulating the welding specifications, such as voltage, existing, and travel rate, helps develop a consistent weld swimming pool that lessens the threat of gas entrapment. Making use of the appropriate welding method for the details product being welded, such view publisher site as changing the welding angle and weapon position, can even more prevent porosity. Regular assessment of welds and immediate removal of any problems recognized throughout the welding procedure are vital methods to prevent porosity and create premium welds.
Significance of Appropriate Welding Methods
Applying correct welding strategies is extremely important in ensuring the architectural honesty and top quality of bonded joints, building upon the foundation of effective porosity avoidance procedures. Extreme heat can lead to increased porosity due to the entrapment of gases in the weld swimming pool. In addition, utilizing the suitable welding parameters, such as voltage, existing, and take a trip speed, is essential for achieving audio welds with minimal porosity.
Furthermore, the selection of welding process, whether it be MIG, TIG, or stick welding, should line up with the particular needs of the job to ensure optimal results. Appropriate cleansing and preparation of the base steel, along with selecting the ideal filler material, are likewise crucial components of proficient welding methods. By adhering to these best techniques, welders can reduce the risk of porosity formation and produce top quality, structurally audio welds.

Checking and Quality Assurance Procedures
Quality assurance steps play an important function in confirming the honesty and dependability of welded joints. Checking treatments are necessary to identify and prevent porosity in welding, guaranteeing the toughness and sturdiness of the final item. Non-destructive screening techniques such as ultrasonic screening, radiographic testing, and aesthetic evaluation are frequently utilized to recognize possible issues like porosity. These methods enable the analysis of weld high quality without compromising the honesty of the joint. What is Porosity.
Post-weld examinations, on the other hand, analyze the final weld for any kind of flaws, consisting of porosity, and confirm check it out that it meets defined standards. Implementing an extensive top quality control strategy that includes extensive testing treatments and examinations is vital to minimizing porosity issues and ensuring the total high quality of welded joints.
Final Thought
Finally, porosity in welding can be a common issue that impacts the high quality of welds. By determining the typical root causes of porosity and executing best techniques for avoidance, such as correct welding methods and testing procedures, welders can ensure top quality and dependable welds. It is vital to prioritize avoidance techniques to lessen the event of porosity and keep the honesty of bonded frameworks.
Report this page