Discover What is Porosity in Welding and Its Impact on Structural Honesty
Discover What is Porosity in Welding and Its Impact on Structural Honesty
Blog Article
Recognizing Porosity in Welding: Discovering Reasons, Results, and Avoidance Techniques
Porosity in welding is a consistent difficulty that can substantially affect the top quality and integrity of welds. As experts in the welding sector are cognizant, recognizing the causes, impacts, and avoidance techniques connected to porosity is essential for achieving durable and trustworthy welds. By diving into the origin of porosity, examining its harmful results on weld quality, and exploring efficient prevention techniques, welders can improve their knowledge and skills to produce high-quality welds regularly. The detailed interaction of factors adding to porosity needs a thorough understanding and an aggressive strategy to make certain effective welding results.
Typical Causes of Porosity
Contamination, in the kind of dust, oil, or rust on the welding surface area, produces gas pockets when heated up, leading to porosity in the weld. Improper shielding happens when the shielding gas, commonly used in procedures like MIG and TIG welding, is incapable to fully protect the molten weld swimming pool from reacting with the surrounding air, resulting in gas entrapment and subsequent porosity. In addition, insufficient gas insurance coverage, commonly due to wrong circulation rates or nozzle positioning, can leave parts of the weld unsafe, enabling porosity to create.
Effects on Weld High Quality
The visibility of porosity in a weld can significantly endanger the general top quality and integrity of the welded joint. Porosity within a weld creates spaces or dental caries that damage the structure, making it much more vulnerable to splitting, corrosion, and mechanical failure.
Moreover, porosity can hinder the efficiency of non-destructive testing (NDT) methods, making it challenging to spot various other problems or suspensions within the weld. This can bring about considerable safety problems, particularly in crucial applications where the structural honesty of the welded parts is extremely important.

Prevention Techniques Introduction
Given the harmful impact of porosity on weld high quality, effective prevention methods are critical to preserving the structural honesty of welded joints. Additionally, selecting the ideal welding specifications, such as voltage, present, and take a trip rate, can help lessen the risk of porosity development. By integrating these prevention strategies right into welding methods, the incident of porosity can be considerably decreased, leading to stronger and much more trusted bonded joints.
Value of Appropriate Shielding
Correct shielding in welding plays a crucial duty in avoiding atmospheric contamination and guaranteeing the integrity of bonded joints. Protecting gases, such as argon, helium, or a mixture of both, are frequently utilized to shield the weld pool from reacting with components in the air like oxygen and nitrogen. When these responsive components come right into call with the warm weld swimming pool, they can trigger porosity, causing weak welds with reduced mechanical homes.
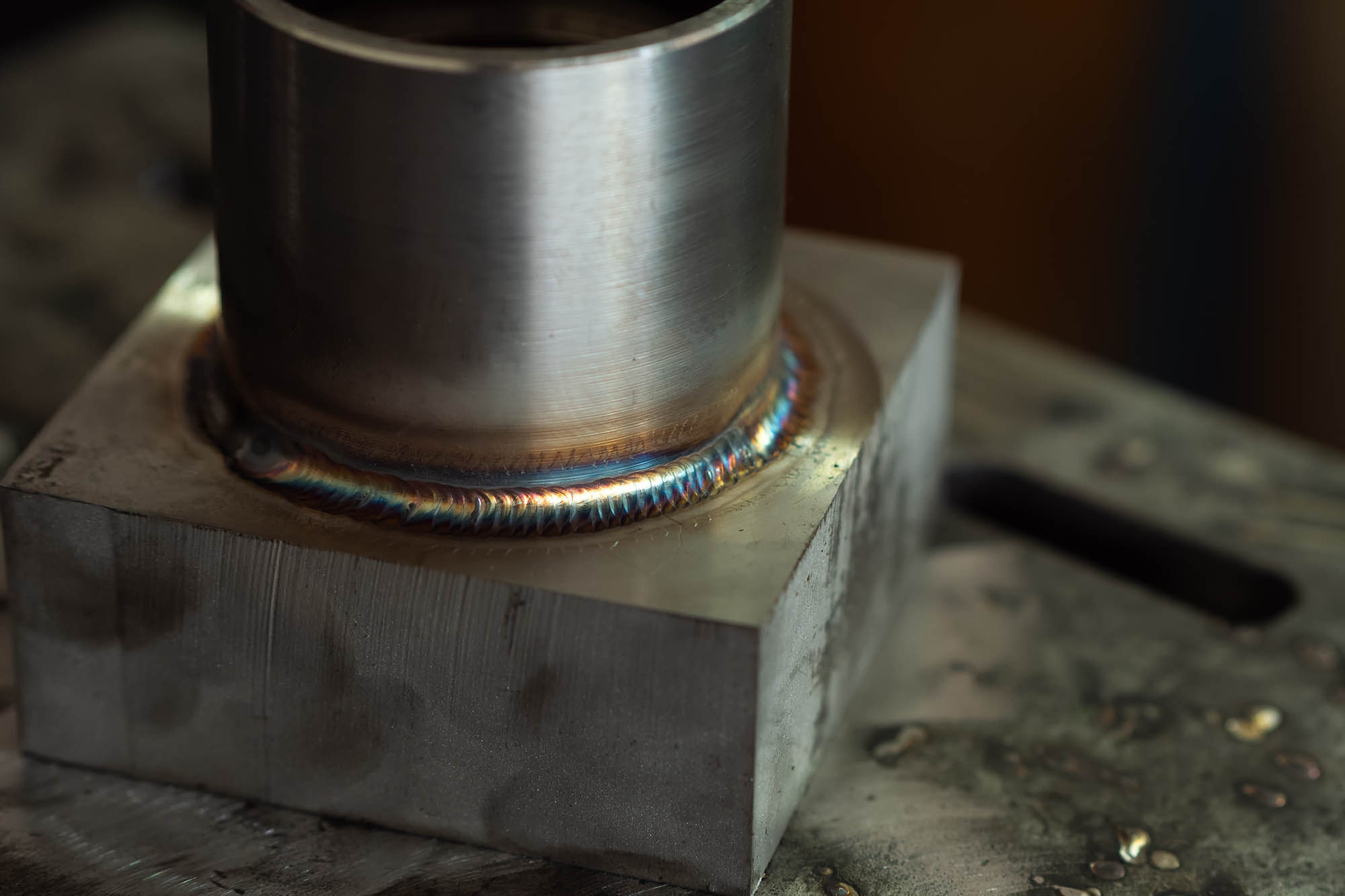
Inadequate protecting can cause different issues like porosity, spatter, and oxidation, endangering the structural integrity of the bonded joint. Adhering to appropriate protecting practices is necessary to produce high-quality welds with a fantastic read marginal issues and guarantee the longevity and integrity of the bonded parts.
Tracking and Control Techniques
How can welders efficiently keep track of and regulate the welding procedure to make sure optimum results and avoid issues like porosity? One trick approach is through using advanced surveillance technologies. These can include real-time monitoring systems that give comments on specifications such as voltage, present, travel speed, and gas circulation prices. By constantly monitoring these variables, welders can recognize discrepancies from the perfect conditions and make instant changes to prevent porosity development.

In addition, applying correct training programs for welders is crucial for monitoring and controlling the welding procedure properly. What is Porosity. Informing welders on the significance of maintaining regular specifications, such as proper gas shielding and take a trip speed, can help prevent porosity issues. Regular analyses and accreditations can also make certain that welders excel in surveillance and regulating welding processes
Furthermore, making use of automated welding systems can improve surveillance and control abilities. These systems can precisely manage welding criteria, decreasing the chance of human error and ensuring constant weld high quality. By combining sophisticated surveillance innovations, training programs, and automated systems, welders can properly check and control the welding process to Go Here decrease porosity defects and achieve premium welds.
Final Thought

Report this page